Ferritic stainless steel
Ferritic
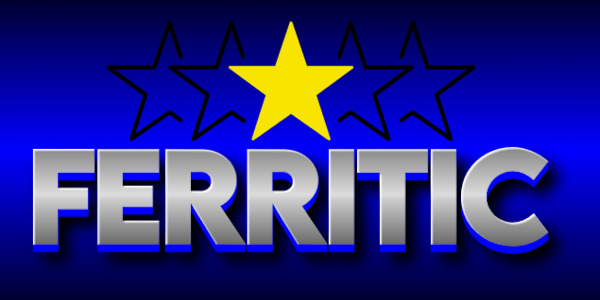
Ferritic stainless steel - ferritic grades of stainless steel are similar in properties to carbon steels, but are corrosion-resistant. They are easy to process. The chromium content is usually 13 - 17%. Such grades are magnetic. These are mainly grades 400 series.
This is one of the most common anti-corrosion alloys. Ferritic stainless steels are represented by a wide variety of grades of different composition and purpose. They all have one common feature - the presence of a high proportion of chromium as an alloying additive.
Ferritic Stainless Steel Frequently Asked Questions
Ferite is a metallurgical phase of iron in which the metallic alloying elements are in solid solution, but the carbon is virtually insoluble. Ferite is virtually absent from hardened martensitic and austenitic stainless steels, but its presence characterizes stainless steels. It is also worth noting that annealed martensitic stainless steels also contain carbide and ferrite.
Ferritic steels have a three-dimensional cubic grain structure, while austenitic and other types of stainless steel have a face-centered grain structure.
The body-centered cubic grain is responsible for the magnetic nature of ferritic steel. This distinguishes it from almost all other types of stainless steel. This difference lies in the quantum mechanical aspect of the metal's microstructure, i.e., how the electrons are arranged in the core of the metal grain.
1. Ferritic steel is resistant to stress corrosion cracking:
- stress corrosion cracking is a common type of degradation of steel caused by a combination of a corrosive environment and tensile stress. Austenitic stainless steels are particularly vulnerable to stress corrosion cracking when exposed to chlorides. However, the microstructures present in ferritic steels give them a high degree of resistance to cracking, making them a good choice for use in environments and structures where chlorides may be present.
2. The steel has good plasticity and formability:
- The hardness of steel depends on carbon, but carbon also makes the steel less ductile and brittle. Because ferritic steel contains a relatively low percentage of carbon, it usually has above-average ductility. This means that ferritic steels can be shaped significantly without the risk of weakening.
The low carbon content of ferritic steels also gives them exceptional formability, allowing them to be formed into a variety of shapes without having to deal with problems such as cracking or necking.
However, the advantages of the low-carbon composition of ferritic steel come with some trade-offs. For example, ferritic steels cannot be strengthened by heat treatment. In addition, some types of ferritic steel may experience problems when welding, such as unexpected cracking along the heat-affected zone.
3. ferritic stainless steel has a relatively low coefficient of thermal expansion.:
- ferritic steels have a naturally low coefficient of thermal expansion. This can be a real advantage and simply means that ferritic steels experience less expansion when they accept heat.
Because the metal more easily maintains its fixed dimension, this makes some ferritic stainless steels well suited for high temperature applications.
4. It has high thermal conductivity:
- ferritic stainless steels have excellent thermal conductivity properties, meaning that heat can pass through them efficiently. As a result, ferritic steels are widely used in furnace and boiler heat exchangers and other heat transfer applications.
5. It has good oxidation resistance:
- Ferritic stainless steel is quite resistant to oxidation, especially at high temperatures. This resistance is a result of the formation of a protective chromium oxide film on the surface of the steel. It is possible to further improve the oxidation resistance of steel by adding silicon and/or aluminum to the composition during the production of ferritic steel.
These elements may include ferromanganese, silicon, vanadium, phosphorus, chromium, ferrophosphorus, manganese, etc. The main role of these alloys is to add the appropriate alloying elements to the molten steel.
1. The first group includes ferritic stainless steels, which are among the cheapest types. They have very low levels of chromium, meaning they tend to accumulate a layer of localized surface rust over time.
2. The second group is the most commonly used grades. Due to the higher chromium content, these steels have greater resistance to corrosion. Ferritic steels of the second group are usually used for building elements and interior equipment.
3. Ferritic steels of group III are well known for their ease of forming and welding, which means they are suitable for a wide range of applications.
4. Ferritic stainless steels of group IV contain higher amounts of molybdenum, which further improves their corrosion resistance. This type of steel is typically used for high-humidity applications such as exhaust systems and hot water tanks.
5. Ferritic steels of group V have the highest chromium content, which gives them a degree of corrosion resistance that is unmatched by all but a few other metals.
- civil engineering;
- architecture and design;
- food industry;
- manufacture of kitchen utensils, tables, serving tools, sinks, showers, parts of washing machines, drums and trays for dishwashers;
- automotive industry (decorative exhaust systems);
- production of external and internal fittings;
- heat exchanger equipment;
- manufacturing of machine parts and equipment for the wine industry;
Some grades of these steels are approved for use in the manufacture of equipment used in the meat and dairy industries at temperatures of 30 - 140 °C, etc.;
- cutting tools (knives, scissors, etc.);
- turbine and boiler parts;
- fasteners, wear-resistant gaskets;
- thermal and separation screens, filters;
- kitchen utensils;
- manufacturing of containers;
- chemical and petrochemical production;
- paper production;
- processing of household and sewage waste;
- mining (and everything connected with it, including mine development).
List of ferritic stainless steel grades
List of stainless steel grades that belong to the ferritic type. To get detailed information about a specific grade, follow the link from the list.
Stainless Steel Grade AISI 403 / 410S | EN 1.4000 | DIN X6Cr13
Ferritic stainless steel EN 1.4000 | AISI 403 / AISI 410S | DIN X6Cr13 with a small addition of aluminum minimizes the formation of austenite at high temperatures, thereby
...Stainless Steel Grade AISI 405 | EN 1.4724 | DIN X10CrAlSi13
AISI 405 | EN 1.4724 | DIN X10CrAlSi13 is a ferritic stainless steel supplemented with aluminum. It is characterized by resistance to sulfur-containing gases. The steel is
...Stainless Steel Grade AISI 409 | EN 1.4512 | DIN X2CrTi12
AISI 409 | EN 1.4512 | DIN X2CrTi12 - is a ferritic grade of stainless steel. Its chemical composition averages 11% chromium and 1% titanium. It is mainly used to produce sheets,
...Stainless Steel Grade AISI 429 | EN 1.4001 | DIN X7Cr14
Stainless steel grade AISI 429 | EN 1.4001 | DIN X7Cr14 is a ferritic steel. It is also known as chromium steel UNS S42900. This steel has good corrosion resistance and its
...Stainless Steel Grade AISI 430 | EN 1.4016 | DIN X6Cr17
AISI 430 | EN 1.4016 | DIN X6Cr17 - is one of many stainless ferritic chromium corrosion-resistant steels that is most widely used. It belongs to the group of general-purpose
...Stainless Steel Grade AISI 430F | EN 1.4105 | DIN X6CrMoS17 | EN 1.4104 | DIN X14CrMoS17
AISI 430F | EN 1.4105 | DIN X6CrMoS17 and EN 1.4104 | DIN X14CrMoS17 are close in chemical composition and some properties to stainless steel grade AISI 430 (EN 1.4016). But there
...Stainless Steel Grade AISI 430FSe
AISI 430FSe is a ferritic stainless steel grade in which sulfur is replaced by selenium to improve machinability. A basic non-heat treatable stainless steel with 17% chromium,
...Stainless Steel Grade AISI 430Nb | EN 1.4511 | DIN X3CrNb17
AISI 430Nb | EN 1.4511 | DIN X3CrNb17 is a type of ferritic stainless steel of the AISI 430 type with the addition of niobium. Niobium provides better resistance to
...Stainless Steel Grade AISI 430Ti | EN 1.4510 | DIN X3CrTi17
Titanium stabilization gives AISI 430Ti | EN 1.4510 | DIN X3CrTi17 steel good resistance to intercrystalline corrosion. In addition, titanium also binds sulfur, which leads to
...Stainless Steel Grade AISI 434 | EN 1.4113 | DIN X6CrMo17-1
AISI 434 | EN 1.4113 | DIN X6CrMo17-1 is a ferritic stainless steel, one of the most widely used ferritic stainless steels. The addition of molybdenum improves the overall
...Stainless Steel Grade AISI 436 | EN 1.4526 | DIN X6CrMoNb17-1
AISI 436 | EN 1.4526 | DIN X6CrMoNb17-1 is a ferritic stainless steel alloyed with molybdenum. It is an improvement of the AISI 434 grade with a small stabilizing additive of
...Stainless Steel Grade AISI 439 | EN 1.4510 | DIN X3CrTi17
Stainless steel AISI 439 | EN 1.4510 | DIN X3CrTi17 is a stabilized nickel-free grade. It is characterized by a high level of resistance to corrosion and oxidation, including sea
...Stainless Steel Grade AISI 441 | EN 1.4509 | DIN X2CrTiNb18
AISI 441 | EN 1.4509 | DIN X2CrTiNb18 is a ferritic stainless steel that has good mechanical strength and oxidation resistance at relatively high temperatures. Compared with most
...Stainless Steel Grade AISI 442 | EN 1.4742 | DIN X10CrAlSi18
AISI 442 | EN 1.4742 | DIN X10CrAlSi18 is a heat-resistant ferritic chromium stainless steel with the addition of aluminum. It is characterized by resistance to sulfur-containing
...Stainless Steel Grade AISI 444 | EN 1.4521 | DIN X2CrMoTi18-2
AISI 444 | EN 1.4521 | DIN X2CrMoTi18-2 - is a low-carbon, molybdenum, titanium ferritic stainless steel. It has better corrosion resistance than conventional ferritic and
...Stainless Steel Grade AISI 446 | EN 1.4762 | DIN X10CrAlSi25
Stainless steel AISI 446 | EN 1.4762 | DIN X10CrAlSi25 is a ferritic stainless steel intended for primary forming into forged products. Its EN 1.4762 counterpart is typically used
...