Heat-resistant stainless steel
Heat resistant
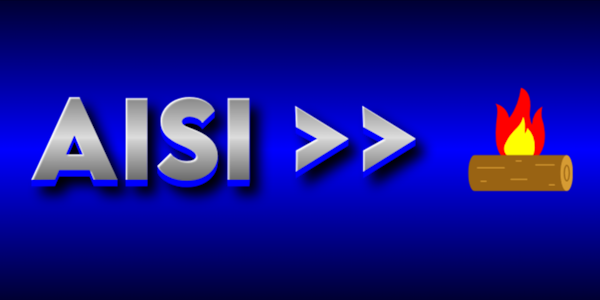
Heat-resistant stainless steel - it is basically an austenitic stainless steel, containing a high content of chromium (20 - 25%) and nickel (10 - 20%) and, as a result, has better oxidation resistance at high temperatures. One defines heat-resistant stainless steels as alloys that are used in temperatures between 500 °C and 1150 °C. In technical language, they are also called heat- and creep resistant.
Frequently Asked Questions About Heat Resistant Stainless Steel
The point is that a metal alloy can have different tolerances to high temperatures depending on whether the exposure is continuous or intermittent. Here are some examples of continuous and intermittent temperature limits for stainless steel:
AISI 304
Continuous: 925°C;
Periodic: 870 °C;
AISI 309
Continuous: 1095°C;
Periodic: 980 °C;
AISI 310
Continuous: 1150°C;
Periodic: 1025 °C;
AISI 316
Continuous: 925°C;
Periodic: 870 °C;
AISI 410
Continuous: 705°C;
Periodic: 815 °C;
AISI 420
Continuous: 620°C;
Periodic: 735 °C;
AISI 430
Continuous: 815°C;
Periodic: 870 °C;
You may have noticed an odd and potentially counterintuitive trend in the 300 series stainless steel alloys listed here. Specifically, their recommended maximum continuous use temperature is higher than their intermittent use temperature limit. It is natural to assume that exposing a metal to high temperatures for a shorter period of time will result in less stress on it than long-term exposure.
When metal is heated, it can expand and then contract as it cools. Also, steel alloys in furnace-like conditions can develop scale on their surface - a kind of flaky substance made up of iron and iron oxide. This substance replaces the outer layer of the metal.
When exposed to high and low temperatures repeatedly, scale can begin to crack and split, weakening the metal's shape. This can happen because of the difference in the coefficient of expansion between the stainless steel metal core and its scale surface. In simple terms, the interior of the metal expands or contracts at one rate, while the scale on the surface expands or contracts at another. This difference causes the metal to begin to disintegrate, layer by layer, until it finally fails completely.
In other cases, you may need to consider the metal's chemical resistance in addition to its operating temperature. This will be able to preserve your structures and parts when exposed to several processes at the same time (temperature and chemical exposure).
List of heat-resistant heat-resistant stainless steel grades
List of stainless steel grades related to heat-resistant, heat-resistant, capable of withstanding permanently or partially high temperature effects. To get detailed information about a specific grade, follow the link from the list.
Inconel 600 | AISI 600 | Alloy 600 | EN 2.4816 | DIN NiCr15Fe | Nicrofer 7216 | Sanicro 70 | UNS N06600
Inconel 600 | AISI 600 | Alloy 600 | EN 2.4816 | DIN NiCr15Fe | Nicrofer 7216 | Sanicro 70 | UNS N06600 is an alloy created for use in service conditions in cases where high
...Inconel 601 | AISI 601 | Alloy 601 | EN 2.4851 | DIN NiCr23Fe | Nicrofer 6023 | Sanicro 61 | UNS N06601
Inconel 601 | AISI 601 | Alloy 601 | EN 2.4851 | DIN NiCr23Fe | Nicrofer 6023 | Sanicro 61 | UNS N06601 is a heat-resistant and corrosion-resistant nickel-chromium metal intended
...Inconel 617 | AISI 617 | Alloy 617 | EN 2.4663 | DIN NiCr23Co12Mo | Nicrofer 5520 Co | UNS N06617
Inconel 617 | AISI 617 | Alloy 617 | EN 2.4663 | DIN NiCr23Co12Mo | Nicrofer 5520 Co | UNS N06617 is a nickel-chromium alloy with additives of molybdenum and cobalt. It has
...Inconel 625 | AISI 625 | Alloy 625 | EN 2.4856 | DIN NiCr22Mo9Nb
Inconel 625 | AISI 625 | Alloy 625 | EN 2.4856 | DIN NiCr22Mo9Nb is a nickel-based superalloy with high strength properties and resistance to elevated temperatures. It also
...Stainless Steel Grade AISI 253MA | EN 1.4835 | DIN X9CrNiSiNCe21-11-2
AISI 253MA | EN 1.4835 | DIN X9CrNiSiNCe21-11-2 is an austenitic high-temperature heat-resistant stainless steel with good oxidation resistance. The steel is designed for use in
...Stainless Steel Grade AISI 304H | EN 1.4948 | DIN X6CrNi18-11
AISI 304H | EN 1.4948 | DIN X6CrNi18-11 is an austenitic grade of stainless chromium-nickel steel with a higher carbon content, which provides it with increased tensile strength
...Stainless Steel Grade AISI 309 | EN 1.4828 | DIN X15CrNiSi20-12
AISI 309 | EN 1.4828 | DIN X15CrNiSi20-12 - is an austenitic high-alloy stainless steel with a large amount of chromium. It has very high corrosion resistance and strength than
...Stainless Steel Grade AISI 309S | EN 1.4833 | DIN X12CrNi23-13
AISI 309S | EN 1.4833 | DIN X12CrNi23-13 is an austenitic stainless steel that provides excellent corrosion resistance and heat resistance, as well as good strength at room
...Stainless Steel Grade AISI 310S | EN 1.4845 | DIN X8CrNi25-21
AISI 310S | EN 1.4845 | DIN X8CrNi25-21 | 20Х23Н18 - is a stainless steel that has high mechanical strength and impact toughness. It has excellent resistance to high-temperature
...Stainless Steel Grade AISI 314 | EN 1.4841 | DIN X15CrNiSi25-20
AISI 314 | EN 1.4841 | DIN X15CrNiSi25-20 - is an austenitic stainless steel that has excellent heat resistance characteristics (heat-resistant stainless steel) among
...Stainless Steel Grade AISI 316Cb | EN 1.4580 | DIN X6CrNiMoNb17-12-2
AISI 316Cb | EN 1.4580 | DIN X6CrNiMoNb17-12-2 - is an austenitic chromium-nickel stainless steel alloy that provides excellent corrosion resistance and increased strength at
...Stainless Steel Grade AISI 321 | EN 1.4541 | DIN X6CrNiTi18-10
AISI 321 | EN 1.4541 | DIN X6CrNiTi18-10 - is an austenitic stainless steel which is able to provide excellent resistance to oxidation and corrosion. It has good creep resistance.
...Stainless Steel Grade AISI 321H | EN 1.4878 | DIN X8CrNiTi18-10
AISI 321H | EN 1.4878 | DIN X8CrNiTi18-10 is an austenitic, heat-resistant chromium-nickel stainless steel which, due to its resistance to scale, is suitable for use at
...Stainless Steel Grade AISI 330 | EN 1.4864 | DIN X12NiCrSi35-16
AISI 330 | EN 1.4864 | DIN X12NiCrSi35-16 is a high temperature, heat-resistant austenitic stainless steel alloy. It is specially designed for extreme performance at high
...Stainless Steel Grade AISI 347H | EN 1.4961 | DIN X8CrNiNb16-13
AISI 347H | EN 1.4961 | DIN X8CrNiNb16-13 is an austenitic CrNi stainless steel with the addition of (Nb) niobium (columbium). The steel provides excellent resistance to
...Stainless Steel Grade AISI 348 | UNS S34800
AISI 348 | UNS S34800 - is an austenitic stainless steel stabilized with niobium (columbium) / tantalum. The alloy has excellent resistance to intergranular corrosion. This steel
...Stainless Steel Grade AISI 405 | EN 1.4724 | DIN X10CrAlSi13
AISI 405 | EN 1.4724 | DIN X10CrAlSi13 is a ferritic stainless steel supplemented with aluminum. It is characterized by resistance to sulfur-containing gases. The steel is
...Stainless Steel Grade AISI 422 | AISI 616 | EN 1.4935 | DIN X20CrMoWV12-1
AISI 422 | AISI 616 | EN 1.4935 | DIN X20CrMoWV12-1 is a high-alloy stainless steel with a martensitic crystal structure and good corrosion resistance. It is mainly used for parts
...Stainless Steel Grade AISI 442 | EN 1.4742 | DIN X10CrAlSi18
AISI 442 | EN 1.4742 | DIN X10CrAlSi18 is a heat-resistant ferritic chromium stainless steel with the addition of aluminum. It is characterized by resistance to sulfur-containing
...Stainless Steel Grade AISI 446 | EN 1.4762 | DIN X10CrAlSi25
Stainless steel AISI 446 | EN 1.4762 | DIN X10CrAlSi25 is a ferritic stainless steel intended for primary forming into forged products. Its EN 1.4762 counterpart is typically used
...
Page 1 of 2