Stainless steel pipe bending is a manual, automatic / mechanical or combined process of metal forming to obtain the desired shape using stainless steel pipe bending equipment, special technical tools or special bending devices.
Stainless steel pipes can be bent to a variety of angles and radii depending on the specific application and the type of pipe being used:
- By shape: round, profile - square, rectangular, oval, flat-oval, special.
- By manufacturing method: welded / seamed, seamless / solid-drawn.
- Depending on the wall thickness: thin-walled, thick-walled.
The process of bending stainless steel tubes usually involves the use of a mandrel to prevent the stainless steel tube from breaking during the bending process. The mandrel provides support for the tube and prevents it from wrinkling or deforming undesirably. In addition, lubricants and cooling methods and means such as water or oil can be used to facilitate the bending process and prevent the stainless steel tube from cracking.
Bending stainless steel pipes, especially at home, can cause some difficulties. To do this, you need to use a specialized tool with a mechanical or electric drive. Using the first requires physical effort, the second - the presence of a network connection at the place of work. It is also important to consider that after deformation, the stainless steel pipe can change its properties and characteristics:
- The cross-section shape becomes ovalized, which can negatively affect the pipe's throughput capacity.
- The outer wall of the stainless steel pipe, which bears the main pressure of the working medium flow, becomes thinner.
- On the inner wall of the stainless steel pipe, irregularities and fractures are formed, which can subsequently cause corrosion.
- The metal of the pipe at the bending point may be slightly or strongly magnetized, even if you use non-magnetic grades of stainless steel.
The process of bending stainless steel pipes can be divided into two types depending on the means: manual and industrial. Depending on the temperature conditions: cold or hot bending of stainless steel pipes.
Cold bending of stainless steel pipe
Cold bending of stainless steel pipe involves the use of auxiliary equipment such as a mandrel, a holder, a machine and other simple tools and equipment.
Manual bending of stainless steel pipe
1. The simplest bending scheme: the simplest bending scheme for a stainless steel pipe consists of two elements rigidly fixed to a certain surface:
- stop - fixes one end of the pipe during bending;
- radius base - the force of the second end of the pipe is applied around it. The geometry of the surface of the radius base, against which the pipe rests during bending, plays the role of a matrix for forming a wall along the inner radius of the bend.
Use proper bending technique:
When bending stainless steel tubing, make sure you apply even pressure to avoid distortion or kinking. It may also be helpful to use a bending mandrel to support the tubing as you bend it and prevent the walls of the tubing from collapsing.
Choose the right type of stainless steel:
Different grades, brands of stainless steel have different levels of ductility, or the ability to deform without breaking. For example, austenitic stainless steels such as AISI 304, AISI 316, AISI 321 are more ductile and much easier to bend than martensitic stainless steels such as AISI 410 and AISI 420.
The final shape of the tube depends on the degree of bending and the bend radius. Bending the tube to a smaller radius requires more force and can result in the tube becoming flattened or deformed.
Be aware of springback: stainless steel tubing, depending on the grade of stainless steel you choose, tends to return to its original shape after bending. This means that the tubing may need to be bent slightly more than the desired final shape to compensate for this springback.
Although the bending procedures for round tubes, rectangular tubes, oval tubes and square tubes are the same, square and rectangular stainless steel tubes require special attention during the bending process.
2. The classic method of manual cold bending is the use of the Volnov machine. This easy-to-use manual machine allows you to bend a stainless steel pipe to the required angle. Its versatility can be increased by using sets of removable rollers.
The design of such a machine is simple:
- stop bracket;
- clamp with handle;
- movable roller;
- bending roller;
- bendable part.
Bending can negatively affect the performance characteristics of a stainless steel pipe, worsen the aesthetic appearance of your structure or product due to unnecessary/excessive deformations during the bending process. Therefore, to prevent unnecessary deformations, you can, for example, use river sand or another filler. The pipe is closed with a plug at one end, and sand is poured into the other end and plugged with a stopper. Then the stainless steel pipe is bent, after which the sand is removed.
3. Bending stainless steel pipe with a mandrel:
This method is well suited for stainless steel pipes with a round cross-section.
A mandrel is a conical tool by which material can be forged, compressed, stretched, or formed, or a flanged, tapered, or threaded rod that grips the workpiece to be machined.
Mandrel bending is a popular method for bending stainless steel tubing because it allows for tight radius bends without compromising the structural integrity of the tubing. In the mandrel bending process, a mandrel is inserted into the tubing before the bend begins. The mandrel is typically made from a harder, stronger material than the stainless tubing and is usually shaped like a cone or layer.
The mandrel provides support for the tubes during the bending process, preventing them from breaking or deforming. This allows for tight radius bends without creases or kinks, which can be especially important in applications where precise tolerances and a smooth surface are required.
It is also important to note that mandrel bending is generally used for smaller diameter tubing. If the diameter of the tubing is too large, it may not be possible to insert the mandrel inside. Additionally, mandrel bending may not be suitable for some types of stainless steel tubing, such as those with very thin walls or those prone to cracking.
To achieve the best results, mandrel bending requires a special machine, which is a tool that can bend pipes with precise control of the bending angle and radius. This type of machine also allows for multiple bends on a single piece of stainless steel pipe.
Bending stainless steel pipe using a mandrel
A mandrel is a special piece of equipment that prevents damage to the pipe during the process. It can be used to avoid a decrease in the thickness of the pipe wall, the appearance of corrugated folds, and distortion of the pipe shape.
Mandrels are one of the main components for high-quality stainless steel pipe bending, and machines that work with a mandrel are called "mandrel pipe benders". There are other types of equipment that are called "mandrelless", meaning that they cannot use mandrels.
Historically, stainless steel pipe bending was mainly done with a filler, usually sand. Sand was poured into the pipe, both ends were welded or plugged and a bend was made. The mandrel plays the role of a filler in pipe bending technology and helps to make a more controlled deformation and prevent problems and ovality of the pipe after bending. The mandrel also stabilizes the pressure of the pipe on the outer wall during bending. The position of the mandrel is adjusted on the pipe bending machine, and different types allow you to perform even very complex types of bending, such as bending thin-walled pipes, small radii and rigid stainless metals. It is also important to note that bending with a mandrel is used in the "winding" pipe bending technology.
Today, for bending technology for all hard materials such as stainless steel, mandrels made of aluminum-bronze alloy are used.
Even for large radii, the mandrel is an element that improves the bending quality. The possibility of using a mandrel or using a pipe bending machine with a mandrel is the only active technology for most bends and is used in all industries. Moreover, this depends on the area of application - for example, for any liquid or air pipelines under pressure, the bending quality is especially important.
The quality of bent stainless steel tubes, as well as their final geometry, is based on the quality outside and the quality inside the bend. The main elements that must be taken into account to ensure quality inside the bend are the fold smoother (blank holder), the mandrel + the capabilities of the physical characteristics of the machine and the properties of the grade of stainless steel from which the tube is made. For ovality, convexities, bellows and deformation areas, the mandrel is the first element that must be installed and adjusted for quality bending.
How necessary is it to have the correct mandrel ?
Depending on the purpose and for complex tasks, even a small positioning of a tenth of a millimeter can change the quality of the bend. Fine adjustment also affects the wear of the main elements of the pipe bending mandrel.
The scope of application of stainless steel pipes is quite diverse. They are used to produce sports ground equipment, lay communications with water or liquid fuel, create parts for the automotive industry, and many other areas.
At the same time, the minimum number of seams and joints makes the entire structure more monolithic, hermetic and reliable. There are often cases when pipelines or other metal structures burst in places of seams, which led to leaks. This can pose a danger to human life and health and harm the environment.
To avoid and prevent this, mandrel bending of stainless pipes often helps, which allows you to give a solid product the desired shape and make a certain bending angle. It is noteworthy that the bending of a pipe on a machine with a mandrel is almost ideal, which cannot be said about simpler models.
It is better to take a pipe bender for thin-walled stainless steel pipes with a protector. It is characterized by high efficiency and low labor costs, as a result of which it is in demand among consumers. However, this machine is not suitable for working with thick-walled pipes.
What are the types of mandrel bending machines for stainless steel pipes ?
According to the control method, the mandrel pipe bending machine can be semi-automatic or automatic. If it is semi-automatic, then it will have to be operated partially manually, that is, physical work is required.
The operation of the automatic equipment is controlled by a CNC machine with a built-in computer. The data on the bending scheme and its numerical indicators are entered there, so one worker is enough to control the functioning of the device.
Although the configuration of stainless steel pipes can be very different, the bending radius of the pipe should not be more than twice the radius of the pipe. At the same time, the reliability and tightness of the design, in which a fitting connection is used instead of bending pipes, will be significantly lower.
Types of design of a pipe bending machine with a mandrel:
- With power supply. Pipe benders of this type have the widest application in various spheres of production. They have fully automatic control. They can provide stainless pipes with quite different configurations with high quality and accuracy.
- Crossbow. Equipped with a T-shaped frame. Consists of a pipe holder and a movable lever installed perpendicularly. A hand tool of this type is capable of bending a pipe at an angle of up to 180°. It is usually used for complex design solutions.
- Hydraulic. There are manual and stationary models. Using a manual mandrel pipe bender, you can shape pipes with a small cross-section. Stationary models are used to work with pipes up to 100 mm in diameter in industrial production conditions. You can bend a pipe on such a machine to an angle of 90º.
Bending a pipe with a mandrel can be performed using different schemes. If hydraulic crossbow or pipe benders are used for the work, then the result is a product that most accurately corresponds to the specified parameters.
Equipment with roller mechanisms bends stainless steel pipes by gradually winding the parts onto rollers. However, machines of this type are only stationary. And if we are talking about conveyor production, then electric pipe benders are used there.
When using a pipe bender without a mandrel, the bend is formed under pressure transmitted to the workpiece by a manual or hydraulic drive. Under the influence of pressure on the pipe, the wall located inside the bend radius begins to deform gradually, forming an angle. The result is a wavy surface. On the opposite side, the metal of the wall stretches and weakens. Bending done in this way leads to a loss of pipe strength and deterioration of its performance characteristics.
But if you use a pipe bender equipped with a mandrel, the process of bending the pipe is carried out as evenly and smoothly as possible, so that the strength of the tube walls over the entire surface is approximately the same.
Hot bending of stainless steel pipe
Bending stainless steel tubing with heat provides a more controlled shape than cold forming. It also helps ensure smooth edges and consistent bends when completing projects. The heat used for bending also helps reduce springback, making it easier to maintain consistent shapes and dimensions. When bending a specific grade of stainless steel tubing, it is important to strictly adhere to the correct temperature, as excessive heat can cause permanent damage to the material. To prevent this from happening, be sure to use a thermocouple or similar device to constantly monitor the temperature of the material.
Using heat to bend stainless steel tubing can be problematic. It is always best to attempt to bend stainless steel tubing when cold, but if you must use heat, heat the tubing to the recommended hot forming temperature for the particular grade of stainless steel and then bend.
Advantages of thermal (hot) bending
Heat bending provides great control over the shape and size of your project parts, making it easy to create complex shapes. You can also use multiple heating elements to bend different parts at the same time, significantly reducing production time. Additionally, if you are looking for greater precision in your bends, heat allows for fine adjustments to achieve the desired shape. Finally, due to the precision and accuracy of using heat bending processes, you can achieve less waste compared to manual methods such as cold forming or press brake.
Disadvantages of hot bending
A serious drawback is the risk of overheating the stainless steel pipe. Overheating can lead to loss of pipe properties: loss of strength, acquisition of brittleness, loss of corrosion resistance in the heating zone. Therefore, when hot bending stainless steel pipes, it is necessary to strictly observe the temperature heating limits for different types of stainless steel.
Bending stainless steel pipe with a pipe bender
A pipe bender or pipe bending machine is a stationary or portable equipment (machine or device) designed for bending pipes of a certain type.
Lever pipe bender
Lever pipe benders can be used to bend stainless steel pipes. This type and its design allow the work to be done using only human muscle power. The advantages of such devices are:
- possibility of bending up to 180 degrees;
- relatively compact size;
- ease;
- ease of use when held in hands or in a vice;
- ease of bending due to the large lever arm;
- adjustable lever position for best bending orientation and force transmission;
- rapid change of design elements;
- relative cheapness;
Manual pipe benders with a mechanical screw rod allow you to bend stainless steel pipes up to 18 mm in diameter at the required angle.
Flaws:
- allows bending of stainless steel pipes of small diameter only;
- It is possible to bend only pipes with minimal wall thicknesses (thin-walled stainless steel pipes);
- there is a risk of corrugated folds appearing at the bend of the pipe.
Bending stainless steel pipe using a crossbow type pipe bender
A widely used pipe bender for stainless steel pipes is a crossbow-shaped device. Its operating principle is that the pipe is placed on two support points rotating around their axes. The bending profile is connected to the rod of a hydraulic or screw jack so that the force is applied to the middle part of the pipe between the support points.
This design allows bending a stainless steel pipe of a fairly large diameter, with a bending angle of up to 90 degrees. Lightweight and compact portable pipe benders of this type allow bending a stainless steel pipe with a diameter of up to 101.6 mm. The bending force is created by a rod of different designs.
Depending on the frame design, there are several types of such a device:
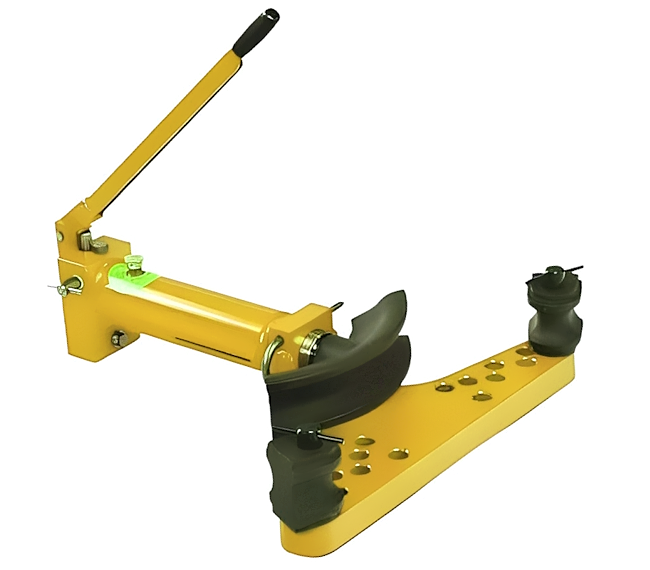
Hydraulic, manual, open frame
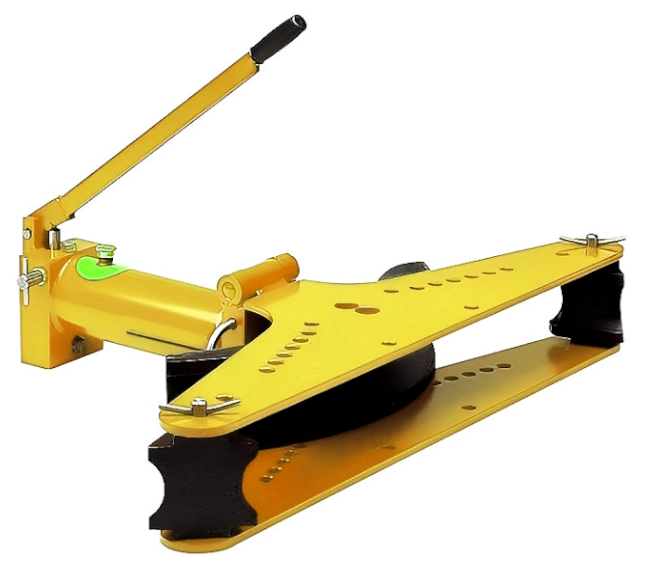
Hydraulic with manual drive and closed frame
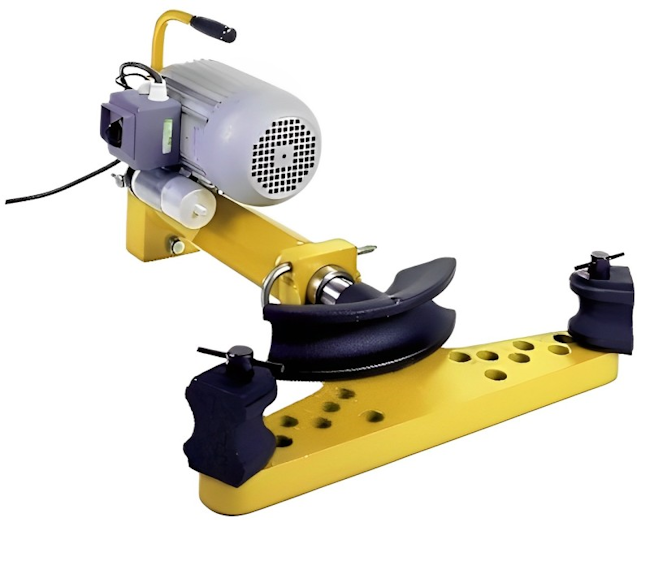
Hydraulic, electric, open frame
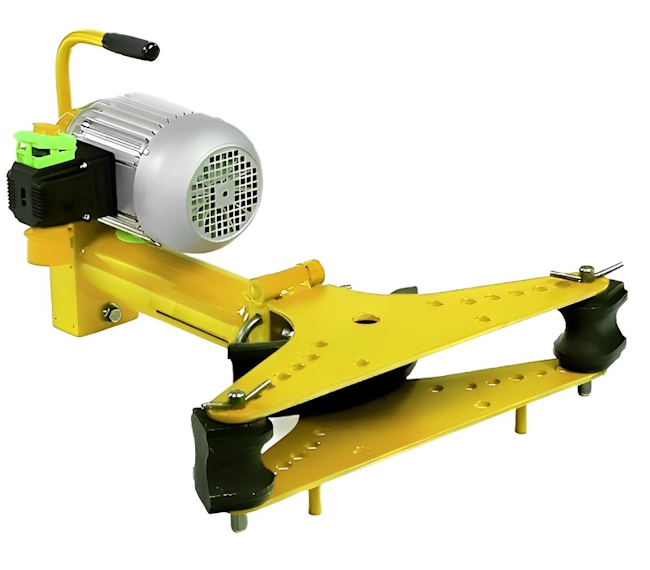
Hydraulic with electric drive and closed frame
Open frame benders are designed for pipes with a diameter of no more than 25 mm. The piston push force does not exceed 80 kN. Similar devices with a closed frame are used to bend pipes with a diameter of up to 101.6 mm. The frame provides increased rigidity during work with high forces. The piston push force reaches 200 kN.
The single-circuit hydraulic system is equipped with a spring, which makes work easier, so you can quickly retract the piston, easily and with maximum precision perform the work. And the presence of an electric drive further simplifies and accelerates it, since no additional physical force is required here.
Bending stainless steel pipe with an electric pipe bender
The most practical devices for bending stainless steel pipes include electric pipe benders. They are light in weight and can be moved from one place to another without additional effort. They can be used directly at the construction or repair site, as well as at the site of the future structure.
This machine is not cheap, but it has its own special characteristics:
- bending angle up to 180 degrees;
- automatic mode (no previous manipulations);
- speed control;
- reverse stroke;
- can be used without a vice anywhere;
- virtually no deformation of the pipe at the bend due to the ideal alignment of the bending segment and the stop;
- smooth feed;
- ease of use;
- quick change of attachments;
- high operating speed;
- compactness;
- light weight;
- high specific drive power;
- versatility - due to the presence of a set of segments and stops for bending various diameters, materials and bending radii;
- high productivity;
- maximum precision of work.
If there is no power supply at the work site, you can use an electric pipe bender with a battery drive:
This is a lightweight, extremely convenient tool for the processing of stainless steel pipes of a certain size. It is characterized by power, high speed with minimal deformation of the walls and cross-section.
Factors affecting the stainless steel pipe bending process
The process of bending pipe, whether hot or cold, changes the properties of the pipe, so various factors must be taken into account when making manufacturing decisions to reduce the amount of distortion in bent sections.
- Wall thickness. Bending a round, square, rectangular or oval (flat oval) stainless steel pipe involves stretching the outside diameter of the bend and compressing its inside diameter. Therefore, a larger wall thickness provides a smaller bending radius and material extensibility with less deformation.
- Bending method. This is a key factor in distortion control. The right procedure can help produce consistent tolerances and accurate parts. Typically, smaller materials require rotary draw bending or pressure bending, which may include erasing dies and mandrels. Induction and incremental bending should be used for larger material bent to a larger radius. The curvature of the structure and the size of the material are important factors in determining the bending method.
- Experience. In many cases, there is no better factor than experience. Many trained benders know what it takes to produce an acceptable product.
- Material size: Larger material bent to a smaller radius is more likely to warp than smaller material bent to a larger radius. Design and planning are needed to help solve bending problems before they occur.
- Tooling. Once the parts have been designed, the bending method selected, and the bending procedures established to the appropriate tolerances, the machine must be set up with the proper tooling. Based on the design conditions, the tools that can be used include a bending die, a clamping block, a follower block, a mandrel, and a die. Some or all of these tools may be required.
- Internal and external lubrication. Oils reduce friction between the tools and the material to be bent. When friction is reduced, the material flows smoothly through the bending equipment, allowing the machine to perform its intended job efficiently.
- Stainless steel grade. Each grade of stainless steel from which the pipe is made has its own unique characteristics of machinability, plasticity, strength. Therefore, a correctly selected grade of stainless steel pipe is the key to success and achieving the desired result in the bending process.
Tips for making custom bends
- Centerline radius. Generally, the minimum achievable centerline radius is one time the diameter of the pipe or tube. If possible, select a centerline radius of 1.5 times or more than the diameter of the pipe. This will save labor costs.
- Wall thickness. When bending tubes, the wall at the outside radius can thin up to 33%, depending on the radius and other factors. You can minimize this thinning by using some bending tools, such as a mandrel, a ferrule. This is important to keep in mind if your application involves high pressure or flow. A thicker wall may be required to achieve the desired results.
- Length of the straight section between bends. Usually the straight section between bends should be two to three times the diameter of the stainless steel pipe, depending on the radius. The exception is the use of arbitrary bending, for which a straight section is not needed.
- Tolerances. The industry standard is ±1 degree bend angle. A tighter standard is ±0.5 degrees. Tighter tolerances, even down to ±0.2 degrees, can be achieved with laser-controlled spring return technology if the program requires it. Linear tolerances are typically ±1.5 mm or less. The industry standard for ovality is 8 to 4%. This can be improved if the application requires it.
What are the methods of industrial cold bending of stainless steel pipes ?
There are several industrial methods of cold bending stainless steel pipes:
- with rolling;
- winding;
- drawing;
- rolling;
- on two supports;
- stretching;
- with internal hydrostatic pressure;
- pushing;
- air.
Bending by rolling
The principle of the method: a rolling roller moves in an arc around a fixed bending roller of the required size, presses the workpiece and performs the bend. In this way, it is possible to bend a pipe with a diameter of up to 150 mm and a significant wall thickness.
Bending by winding
The method has become widespread in large-volume pipe blank shops. This method can bend pipes with diameters from 10 to 426 mm in different planes. To maintain the round shape of the inner section of blanks, calibrated (mandrel) plugs are used, solid in the form of a rod or components. The simplest mandrel for pipes up to 32 mm in diameter can be a steel rope, one end of which is fixed in the handle, and the other is connected to the wire for pulling the rope. The diameter of the mandrel should be 0.1 - 0.5 mm less than the inner diameter of the pipe. When working with a mandrel, nicks and burrs may appear on the inner surface of the pipe due to high contact forces. This is most often observed when bending pipes made of stainless steel with low ductility. Prevention of these drawbacks is achieved by appropriately choosing the mandrel material, the cleanliness of its surface and lubrication. It is better to lubricate the inner and outer walls of the blank. To do this, short pipes are immersed in a bath of oil before bending. It is better to supply lubricant to the bending point of a long pipe, remote from its ends, through the holes in the mandrel. Machine oil or anti-corrosion soap emulsion is used for lubrication.
Bending on two supports
The stainless steel pipe is placed on two supports that rotate around their axes as the workpiece bends. The bending template is connected to the hydraulic or screw jack rod so that the bending force is applied inside the pipe between the supports. This method can bend pipes up to 351 mm in diameter. This type of equipment is especially convenient when pipeline elements need to be bent directly on the construction site.
Roll bending
It is used to bend a small diameter pipe into a ring or spiral. On bending rollers, the workpiece moves in the direction of rotation of the rollers and acquires a curvature determined by the mutual arrangement of these rollers.
Bending by drawing
A thin-walled welded stainless steel pipe or a seamless stainless steel pipe can be bent by drawing. The essence of the method is that a pipe of a larger diameter than required and of a longer length is taken as a blank. The end of the blank is compressed to the required diameter, then penetrates the die and is held by a clamp fixed to the bending template. By rotating the template, the stainless steel pipe is pulled through the die and simultaneously bent around it.
Bending with stretching
The advantage of this method is that it reduces the possibility of deformation of the inner wall of the pipe at the bending point. In this case, the pipe is fixed at the edges, stretched and simultaneously bent by pushing out the bending template.
Bending with internal hydrostatic pressure
A liquid is pumped into the pipe, at the end of which plugs are pre-inserted. As a result of the stresses arising in the wall, the stainless metal reaches a state close to plastic. Then a bending template is brought to the bending point, bending the stainless pipe.
Push bending
It is mainly used to bend stainless steel pipes with a diameter of 5 mm to 10 mm. The method involves pushing the workpiece through a movable and fixed matrix. The amount of matrix clearance relative to each other determines the curvature of the bend. This method can make up to 20 bends in different planes on one pipe.
Air bending
Air bending is a method of bending stainless steel tubing that uses a press brake and punch to form a bend in the tubing. The punch is pressed against the tubing, causing it to bend to the shape of the punch. This method is considered faster and more efficient than other bending methods, but it may not be as precise.
The press brake uses a punch that is pressed against the stainless steel tube, causing it to bend around the punch. The upper die is also part of the press brake, which is the surface against which the punch presses the material to form the tube. The accuracy of the bend is determined by the accuracy of the punch and die, and the process can be adjusted to create the desired bend angle.
One of the main advantages of air bending is its speed and efficiency. The process can be performed quickly and with minimal setup time, saving time and money in large-scale production. In addition, press brakes can be made in different sizes, allowing for bending of pipes of different diameters and thicknesses.
However, air bending has its limitations. It is not as precise as other methods such as mandrel bending or draw bending. The punch and die are the determining factors in bending accuracy, and air bending can result in a wider bend radius than desired. In addition, air bending can result in a slight rounding of the inner bend radius (called “spring return”), which can affect the accuracy of the final product.
The described methods of pipe bending are effective in industrial production and construction conditions and allow obtaining high-quality results regulated by industrial standards.
Induction bending of stainless steel pipe
Induction bending (a type of hot bending) can be a controlled way of bending stainless steel tubes by applying temperature heating using reduced high-frequency electrical energy. Induction technology, originally used for surface hardening of steels, once applied to bending tubes, essentially consists of a coil placed around the tube to be bent. The coil heats a thin section of the tube around its circumference to a controlled, required temperature depending on the type of grade being formed. As the correct bending temperature range is reached, the tube is slowly pulled through the coil while the bending force is applied using a lever with a set radius.
The induction bending process is the most common method for producing long stainless steel bends. This process uses coils in which electricity flows through wires and creates induction in the center of the coils. This large amount of electricity on the coils also results in high heat in the center of the coils. The induction bending process essentially uses inductors to locally heat the parts. The desired shape and angle of the stainless steel bend is maintained by a fixed radius arm. When the stainless steel tube reaches the desired temperature, it is pulled out of the coil while the fixed arm bends the hot spot. Induction bending processes can be used for a variety of applications. Bent products are commonly used in the petrochemical, chemical, shipbuilding, construction, and power industries. Almost any type of stainless steel can be shaped using induction bending machines.
Advantages of induction bending of stainless steel pipe
Compared with other forming processes, induction bending offers several advantages:
- The induction bending process is highly cost effective. Bends can be produced faster than standard components that require additional welding to join.
- Instead of bends (elbows) you can use bends of a larger radius. This reduces wear, and friction also dramatically reduces the pump's performance.
- The use of induction bent components reduces welding requirements.
- The bent parts do not have welded beams on the contacting ones. This significantly increases the homogeneity of stainless steel, which improves mechanical properties.
- The need for non-destructive testing is reduced by using induction bending. This also reduces the overall cost.
- Bends are generally stronger than elbows because the wall thickness of bends is uniform and nearly the same at every point.
- There is no need for lubricants as induction bending is a clean process.
- No additional or filler materials are required during the process. The induction bending process uses only straight pipe.